The Middle East, and in particular, Abu Dhabi, are at the epicentre of global sulphur and sour hydrocarbon production, making this the ideal location to host this premier event that will gather representatives from along the entire sour gas / sulphur value chain to promote technology and innovation, lessons learned, best practices, knowledge transfer, and R&D.
MEScon is devoted to networking, thought leadership, innovation and best practice operations across the entire sour gas and sulphur value chain. With the region’s prominence in the global sulphur industry, MEScon is the place where the sulphur and sour gas community meet to discuss and debate the key strategic themes that are driving the industry.
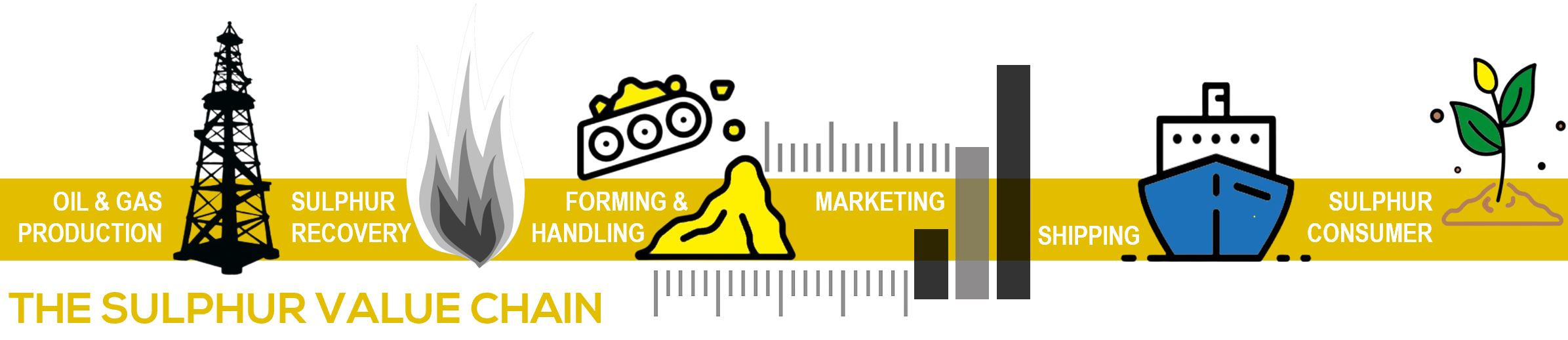
The partnership of CRU and UniverSUL Consulting combines the respective strengths of market-leading analysis and technical expertise, which is reinforced by the support of host sponsor, ADNOC, a recognised leader in the production of sour gas and sulphur. Collectively, this partnership enables a unique event that incorporates the market dynamics and technical and operational aspects of the entire sulphur value chain from sour gas processing through sulphur recovery to transportation, marketing and end uses.